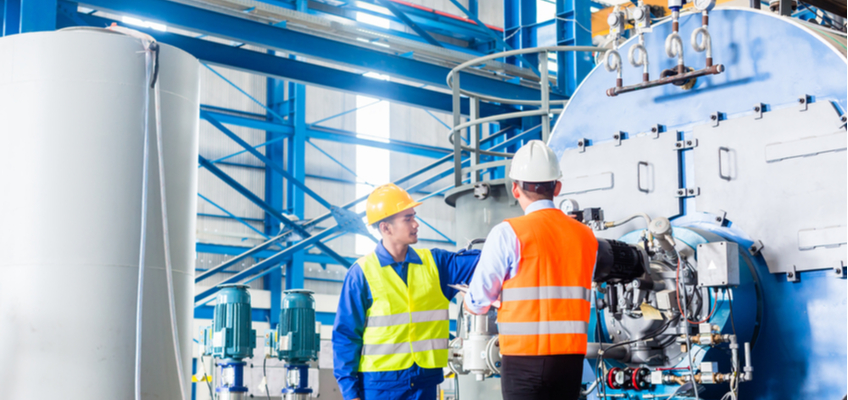
How the Coronavirus (COVID-19) Impacts Manufacturing in Asia
Editor’s Note: This is a guest post by Swedish entrepreneur, Fredrik Gronkvist.
The coronavirus outbreak has resulted in a major disruption for manufacturers in Asia and its customers. In this article, Fredrik Gronkvist shares his experiences dealing with supplier delays, risks, and uncertainty caused by the COVID-19 outbreak.
1. Factories had a Late Start This Year
The coronavirus outbreak occurred just as suppliers were shutting down for the lunar new year holiday. The lunar new year is a major disruption for manufacturing across Asia. Only that this time it got a lot worse.
Normally, we would have expected suppliers to get back to work during the 2nd or 3rd week of February. However, the COVID-19 outbreak prevented factories from reopening until they got the green light from the local government.
As a result, many factories didn’t resume operations until the first week of March. All in all, production has been shut down for up to 7 weeks. That’s a big problem if you’re an Amazon seller or importer relying on your Chinese factories to supply you with products.
Summary
- COVID-19 delayed factories from reopening for 2+ weeks
- Some importers and Amazon sellers are running out of stock
2. Things are Moving Forward, but Slowly
As I write this, most suppliers in our network have resumed operations, and some are already back in production. That said, few manufacturers are operating with a full workforce – resulting in everything moving forward much slower than normal.
This is not necessarily only a result of the virus outbreak, as some workers decide to simply go elsewhere. Either way, everything takes more time. Be it getting a technical drawing from a mold manufacturer, or resuming production for goods left unfinished before the holiday.
When I asked a Chinese sales rep working for a factory outside Shanghai why he hadn’t sent us an invoice, he explained that he and the other office workers had to help out on the production lines. Material and components suppliers are also causing serious disruptions. For example, a Wristwatch consists of many different parts and materials, procured from several different suppliers. Prototypes can’t be made and mass production can’t resume if a certain component is unavailable.
Summary
- The backlog of orders is already a drain on the system, but this year it’s even more severe
- Factories have reopened, but few are operating with a full workforce
- Delays at one factory can disrupt the entire supply chain
3. Trade Shows are Either Delayed or Canceled
Global sources recently announced the cancellation of their April 2020 trade shows in Hong Kong. Given the current travel situation, I think they made the right decision. This is not only a problem for buyers and manufacturers but also service companies like us.
Many of our old and new customers passing through Hong Kong visit our office at the same time. This spring we’ll probably not see much of that. The Hong Kong Trade Development Council (HKTDC) has also rescheduled some trade shows from March to late Spring. However, the Canton Fair is still reported to go ahead in April as planned.
Summary
- Hong Kong trade shows are either delayed or canceled
- The Canton Fair may go ahead as planned
4. Suppliers Outside China are Also Affected
Delays in Mainland China also disrupt supplier networks outside its borders. The South China Morning Post (SCMP) recently reported on how Vietnamese factories in the garment and electronics industry face material and component shortages. This is hardly surprising, given that China is Vietnam’s largest trading partner.
Vietnam is hardly the only country in Asia being affected. Manufacturers in all industries are affected to some extent in the region. Some have also pointed out the risks of relying on China as a manufacturing country. There might be some merit to that, but I don’t think a significant number of buyers will shift orders to factories in other countries for the sake of COVID-19 alone.
Not only because the situation is not limited to China, but also because it would take months to get new molds and tools made – assuming you can even find a new supplier to make your products outside China.
Buyers that will end up shifting production to other countries in the coming months and years would likely have done so either way.
Summary
- Suppliers in other Asian countries are also affected
- Sourcing outside of China is not a quick fix
5. Increased Risk of Supplier Bankruptcy
Chinese factory owners never had it easy, but now might be the hardest time some of them have ever faced. Most factories operate on low-profit margins, leaving them with limited cash reserves to weather a storm like this. Without a steady stream of new orders coming in, they may not be able to stay in business.
Many Chinese factory owners started out during the boom years in the 90s and 00s. They aren’t getting any younger and might decide that it’s time to call it a day. Either way, both scenarios pose serious risks for Amazon sellers and importers. It’s hard to know if your supplier is going out of business (voluntarily or not). Either you put all orders on hold, only to be left without stock, or you take a risk and place another order.
- Some factories may run out of money
- Some factory owners may decide to stop operating
About Chinaimportal.com
Chinaimportal.com provides articles, eBooks, webinars and other resources helping importers better understand product development, sourcing, regulations, risk management and other importing related topics.